This use case examines the requirements of centrifuge and how using custom, or stand alone machine controller, will help give your application a high speed Brushless DC rotation while maintaining perfect position registration.
Application Challenge
Centrifuges are common elements of many medical and biotech laboratory instruments. They require very high rotation speeds, and often have a need for positioning to receive, and deliver, samples. Quadrature encoders give the lowest cost, but will we lose quadrature counts at high speeds?
Application Considerations
Feature/Function |
Units |
---|---|
Speed |
20,000 RPM |
Controller architecture |
Single axis module |
Motor Type |
Brushless DC |
Required Motor Power |
350W |
Motion Control Solution
The diagram below shows an ION® 500 Digital Drive module connected by RS-485 serial to a host PC. A 60V BLDC motor will be driven using Field Oriented Control (FOC) to maximize speed. The motor will utilize a low-cost quadrature encoder with index signal to provide automatic on-the-fly position correction. Using the ION, position profile mode will be used throughout to execute the spin profile and land the samples to an exact destination.
Motion Control Components
Components |
Specification |
Description |
---|---|---|
Motor: |
350W Brushless DC motor |
Permanent Magnet Brushless DC motor with 1,024 count encoder |
Controller: |
ION 500W Digital Drive |
Provides RS-485 communications, Field Oriented Control, position control, encoder feedback and quadrature auto-correct feature |
Hardware: |
Centrifuge with optical home sensor |
Top speed 20,000 RPM, encoder directly encoder motor angle. Home sensor initializes position reference. |
Field Oriented Control
Field Oriented Control (FOC) provides a significant advance over Hall-based control in the area of efficiency and top speed. Typically, top speeds are improved 10-15% using FOC, which utilizes special mathematical transforms to determine an optimum multi-phase vector command at a given moment in time. The ION manages all of these details automatically. The user simply specifies the desired speed profile and destination position.
Figure 1: Field Oriented Control
Automatic Position Correction
Quadrature encoders may occasionally lose position counts during high speed motion. In position-sensitive applications, these small errors can eventually accumulate and result in mis-registration. The solution is on-the-fly position correction using an index signal. Upon power up, the ION automatically records the location of the first index, and thereafter makes small adjustments as needed to eliminate encoder count losses.
Figure 1: High-speed Centrifuge motion control application
The figure above shows an ION Digital Drive, which contains a single-axis motion controller and digital amplifier, driving the centrifuge. The centrifuge provides quadrature A, B, and Index signals, and a home signal is input to the ION to reference the axis after power up.
All ION Digital Drives provide high performance motion control supporting multiple motor types including DC brush, Brushless DC, step, and microstepping motors, and are based on PMD’ Corp.s Magellan®Motion Processor, which provides user‐selectable profile modes including S‐curve, trapezoidal, velocity contouring, and electronic gearing.
You may also be interested in:
- Optimize Control of Syringe Dispensing Application
- Field Oriented Control (FOC) - A Deep Dive
- S-Curve Motion Profiles - A Deep Dive
- Servo Tuning Deep Dive: Black art, rocket science, or walk in the park?
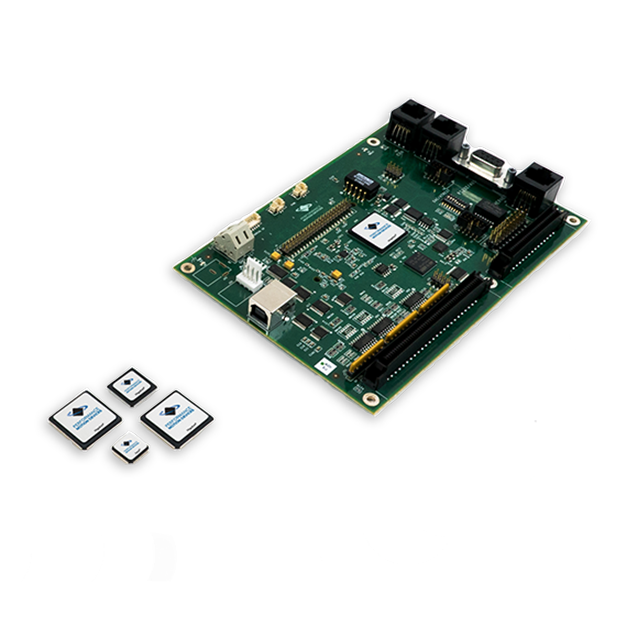
Stay ahead of the competition.
If your existing equipment needs a performance boost or if you need to develop a new product in the shortest development time possible, learn about motion control solutions from Performance Motion Devices.
- 2X faster development
- Motion solutions from ICs to turn-key boards
- Easy to implement
- Always supported