Don't settle for anything less than high reliability, programmability, and precision velocity control when you are designing a high-performance fluid handling application.
Application Challenge
Delivering fluids precisely and safely is a key task for a wide range of medical and pharmaceutical applications, including patient fluid processing, drug delivery, and laboratory diagnostic equipment. Owing to their ability to pump fluid without contamination, peristaltic pumps have long been a favorite for this task. But, how do we build a compact, low-cost motion controller that delivers innovative, reliable capabilities for peristaltic pumps, such as programmable pump profiles, ultra-precise fluid delivery, very wide pumping range, and extensive safety controls?
Application Considerations
Feature / Function
Description
# of Pumps
Three
Velocity Precision
+/- .175%
Dynamic Ranges
1 : 2,500 pump rate range
Actuator Type
Three-phase Brushless DC (BLDC) motor
Figure 1: System Diagram
Motion Control Solution for Peristaltic Pumps
In this application a three-axis Magellan® IC is coupled with three Atlas® Digital Amplifiers to provide very high performance velocity control of Brushless DC (BLDC) peristaltic pump motors. As the system diagram above shows, an ARM microprocessor provides overall motion control of the profiles and sequences. The Magellan motion processor inputs these profile commands and performs position and velocity control. The Atlas Digital Amplifier provides high-performance torque control of each motor along with continuous temperature and current drive monitoring.
The ARM microprocessor communicates by serial RS-485 to the high-level machine controller which in turn manages user input and display. One of six pre-programmed fluid delivery profiles are executed, with the profiles being stored in NVRAM for an update as desired by the high-level machine controller. Velocity profiling commands are sent to the Magellan for each axis. Both velocity and acceleration are commanded on the fly to construct complex velocity profiles, while point to point S-curve profiles are used for delivery of discrete volumes of fluid.
The Magellan inputs the high-level command profiles and generates continuous, smoothly varying profiles that are updated as often as 3,300 times per second. The Magellan accepts encoder feedback as well as Hall Sensor inputs from each motor. The Magellan's tracking window feature is used to signal higher than normal tracking errors, possibly indicating events such as clogging, tube misalignment, or excessive bearing friction.
In combination with the very high precision torque control provided by the Atlas amplifier and the 32-bit profile registers and fast update rate of the Magellan IC, this motor control design easily achieves the target velocity accuracy of +/- .175%.
The Magellan connects to the Atlas Amplifier via an SPI (Serial Peripheral Interface), sending continuous torque commands at a rate of 10,000 updates per second. Atlas, in turn, uses its high precision circuitry to control the current in each phase of the BLDC motor. Internal temperature as well as over and under voltage bus supply conditions are monitored continuously, along with several other conditions. In this application, each Atlas is driven at 24V and delivers 5.5 amps Arm, 10 amps peak. These figures are comfortably within Atlas' overall performance range of up to 14 Arms continuous, 12-56V supply.
PMD Corp's Pro-Motion® Windows-based software package allows Magellan and Atlas to be tuned and optimized for each new pump configuration quickly and easily. High speed trace of servo parameters allows even the most demanding profiles to be analyzed and optimized.
Going Further
The control system described above operates with Brushless DC motors. Both Magellan and Atlas units can be purchased for DC Brush motor control with no software changes or other package reconfiguration of the controller. Similarly, for step motors, both Magellan and Atlas can be configured without change of the moton profile commands. In step motor mode the Magellan IC can still accept quadrature encoder feedback, which may be used to verify position in applications where 100% position confirmation is required.
Solder high-performance and safety right onto your control board
Atlas® Digital Amplifiers are compact single-axis amplifiers that provide high performance torque control of DC Brush, Brushless DC, and step motors. They are packaged in a compact solderable module and utilize standard through-hole pins for all connections.
Multi-axis positioning that delivers precision, speed, and reliability
Magellan® Positioning ICs provide high-performance chip-based motion control for multiple motor types, such as Servo motors and drives. Available in 1, 2, 3, and 4-axis versions, these flexible, programmable multi-axis controllers work with Brushless DC controllers, stepper motors, and DC Brush motors. These ICs are designed for demanding applications such as medical lab automation robotics, liquid handling, and other scientific instrumentation.
You may also be interested in:
- Optimizing A Control Architecture for High Accuracy Syringe Dispensing
- Keep Your Step Motor Position with A Closed Loop Motion Control System
- Digital Current Loop Significantly Quiets Step Motor Noise
- Improving Liquid Handling Robot Throughput by means of Direct Path Planning and Obstacle Avoidance Programming
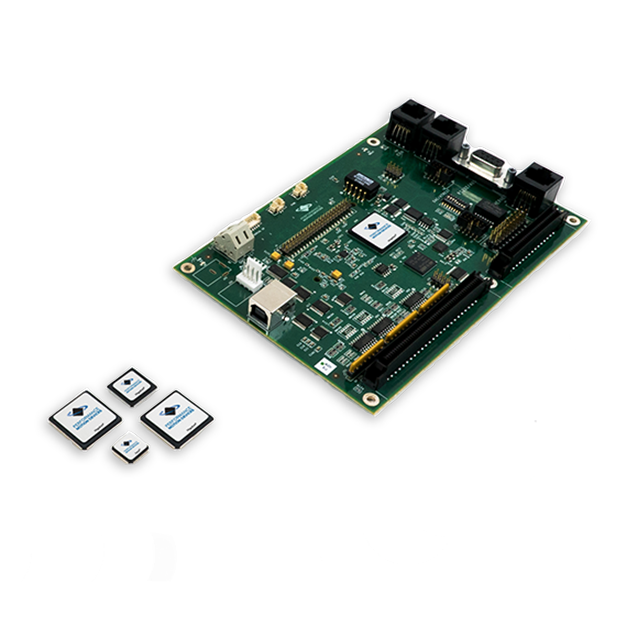
Stay ahead of the competition.
If your existing equipment needs a performance boost or if you need to develop a new product in the shortest development time possible, learn about core advantages of using motion control products from Performance Motion Devices.